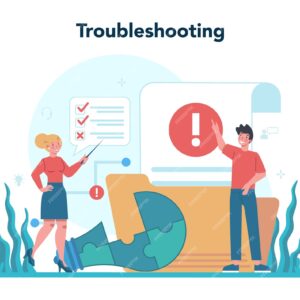
A Step-by-Step Guide to Systematic Troubleshooting in Manufacturing In any manufacturing environment, downtime can be a significant disruptor, affecting production schedules, safety, and the bottom line. When machines or systems malfunction, quickly identifying the cause of the problem and implementing... Read more

FTA is a systematic and structured approach used to identify potential causes of failure and assess the risk of undesired events in complex systems. By visually mapping out the relationships between failures, FTA enables organizations to proactively address vulnerabilities before... Read more
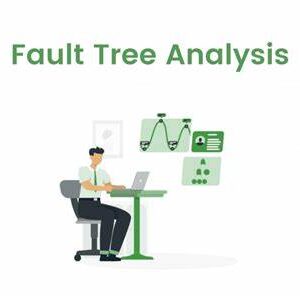
What is Fault Tree Analysis? Fault Tree Analysis (FTA) is a top-down, deductive failure analysis method used to understand the causes of system failures. The analysis begins with identifying a particular undesired event (often referred to as the “top event”),... Read more
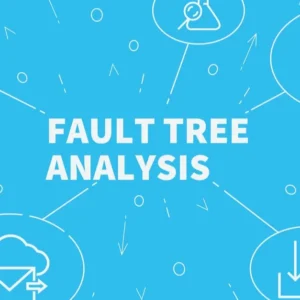
What is FMEA (Failure Mode and Effects Analysis)? Failure Mode and Effects Analysis (FMEA) is a systematic, structured approach used to identify potential failure modes within a system, product, or process and evaluate their consequences. The goal of FMEA is... Read more
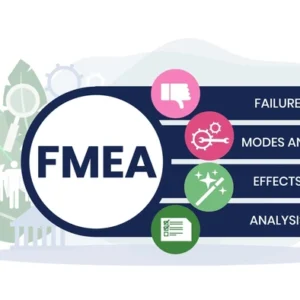
What is FMEA? Failure Mode and Effects Analysis (FMEA) is a methodology used to identify and evaluate potential failure modes within a system, product, or process. The goal is to prioritize the failure modes based on their potential impact, likelihood,... Read more
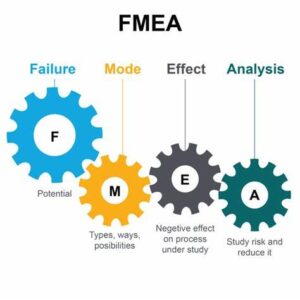
What is FMEA? Failure Mode and Effects Analysis (FMEA) is a systematic method for evaluating the potential failure modes of a product, process, or system. By identifying possible failure modes, analyzing their consequences, and assessing the risks associated with them,... Read more

In the world of engineering, reliability plays a critical role in ensuring that systems and equipment function as intended without unexpected failures. One of the key tools used to model, analyze, and improve system reliability is the Reliability Block Diagram... Read more

In the world of industrial operations, predicting when equipment will fail can make the difference between maintaining smooth operations and dealing with costly downtime. The ability to anticipate failures before they occur can save businesses significant amounts of money and... Read more

In today’s competitive industrial landscape, maximizing equipment performance while minimizing operational disruptions is critical. Companies are continuously looking for strategies to improve productivity and reduce costs. One highly effective strategy that has gained significant traction across various industries is Reliability-Centered... Read more

In the world of manufacturing, engineering, and IT systems, understanding key performance indicators (KPIs) related to system reliability is crucial. Two such important metrics are MTBF (Mean Time Between Failures) and MTTR (Mean Time to Repair). These metrics play a... Read more